Case Study: Near Realtime Replenishment Planning
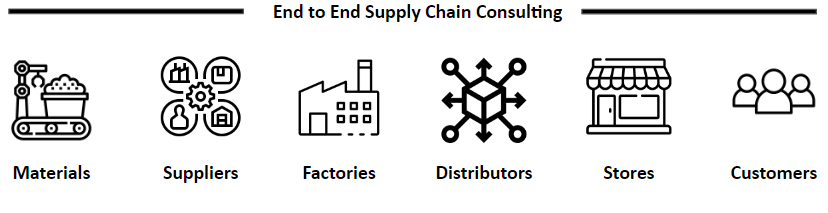
Case Study: Replenishment Planning for a Distributor with a Complex Network
In this case study, we explore how we helped a distributor that manages extensive inventory across a vast network improve their replenishment planning process. While the company was good at filling orders, they knew there was a better approach that could fill orders quicker, optimize inventory, and increase customer fill rates. By implementing a linear programming optimization engine, we helped them streamline operations, reduce costs, and increase efficiency.
Project Goals
The goals of the project were:
- Automate replenishment planning to free up employees’ time, reducing labor costs by hundreds of thousands of dollars annually.
- Ensure a more consistent and data-driven approach to allocating inventory to customer orders.
- Reduce inventory carrying costs by improving stock alignment with customer demand, leading to better cash flow and reduced excess inventory.
Project Background
![]() |
Large-scale distribution network – The distributor manages hundreds of thousands of unique items across approximately 20 distribution centers (DCs) in the US and Canada. The network consists of primary distribution centers along with smaller cross-docking facilities. While replenishment can be fulfilled from multiple locations, network priorities are established to favor specific sites over others to improve efficiency and optimize inventory flow. |
![]() |
Frequent order fulfillment – With short lead times, orders are released to warehouses multiple times a day, requiring a highly responsive and efficient replenishment process. The network operates on a follow-the-sun model, leveraging 24-hour operations across the country to ensure continuous order fulfillment and inventory availability. |
![]() |
Complex sourcing and demand prioritization – The nimbleness of the operations also introduced complexities such as circular sourcing, near real-time demand requirement, and a complex demand prioritization process. |
![]() |
Reliance on manual processes – The existing system combined ERP custom code with manual updates, requiring employees to augment the daily cutoff process—a high-pressure, time-sensitive window where orders were processed in a frantic rush. While this approach ensured orders were fulfilled, it was inefficient and often led to suboptimal inventory allocation. |
Project Solution
The solution uses a linear programming optimization engine to solve the problem. LP optimization engines are fickle but balance constraints, priorities, and objective functions to drive to a near optimal solution which is significantly better than what people can do with a large network.
![]() |
Data Ingestion – The engine ingests customer orders, forecast, inventory, scheduled receipts, purchase orders, the sourcing network, and other relevant data sources. |
![]() |
Demand Prioritization – After ingestion, customer orders are prioritized according to key business rules such as hard allocations, customer priority, adherence to forecast, and past order cuts. |
![]() |
Optimization & Inventory Matching – Prioritized demand is processed by the LP optimization engine, which allocates inventory, inbound shipments, and purchase orders to fulfill orders. The system also suggests transfer orders when necessary. |
![]() |
Post-Optimization & Continuous Execution – If an order is cut, the system assigns a reason code so sales representatives can explain to customers. The optimization process runs multiple times per day, ensuring warehouses can continuously fill orders efficiently. |
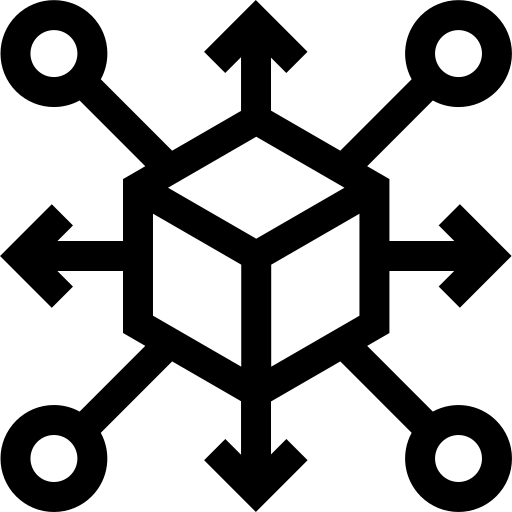
Key Challenges and Solutions
Solving this problem was not simple, but the results save millions of dollars a year. Below are some of the main challenges the team faced in the project.
1. Addressing Circularity Issues: The distributor’s network had circularity where sourcing could draw from reciprocal locations. For instance, Site A could source from Site B, and Site B could source from Site A, creating potential loops that would cause issues for automated planning algorithms. To resolve this, the team introduced virtual locations into the network. By assigning a weighted preference to source items from a primary location first and only turning to secondary locations when necessary, the LP optimization engine effectively minimized circular sourcing conflicts.
ITEM | SOURCE | DEST | TRANSMODE | PRIORITY |
---|---|---|---|---|
1234 | Houston | Dallas | Truck | 1 |
1234 | Dallas | Houston | Truck | 2 |
2. Optimizing Demand-Supply Matching: To allocate products efficiently to customers, multiple tiers of demand classification were implemented. The project leveraged the solver to optimize the demand-supply match across the network. This solver accounted for factors such as inventory levels, transportation costs, and customer demand, ensuring that products were distributed in a way that maximized overall efficiency and minimized costs.
ITEM | LOCATION | CUST | QUANTITY | ORDERID | SHIPDATE | TIER |
---|---|---|---|---|---|---|
A1 | Houston | CUST1 | 100 | 0001 | 8/5/2024 | TIER 1 |
A1 | Houston | CUST2 | 150 | 0002 | 8/5/2024 | TIER 2 |
3. Achieving Order-Level Transfer Visibility: Given the sophistication of their fulfillment process, inventory transfers could not be lumped into a single transfer and had to maintain order-level transfer visibility. The solution needed to handle cases where transfers between distribution centers were often cross-docked, meaning they were not taken off the truck but directly transferred to fulfill orders. This level of visibility allowed the distributor to manage inventory more effectively, reducing delays and ensuring timely deliveries.
4. Near Real-Time Optimization and Execution: One of the most significant challenges was the need to run the optimization in near real-time. Due to a tight order cutoff window, the team needed to ensure that cuts and orders reached the warehouse within an hour. This requirement necessitated multiple optimization runs per day to accommodate different time zones, a sharp departure from the traditional overnight batch processing typically used in replenishment planning. This new approach aligned closely with the operational needs of many consumer packaged goods (CPG) companies and distributors, who require a more responsive and dynamic planning process.
5. Planning Optimization Process: The replenishment planning run was designed to operate seamlessly, much like an Azure or Google function. The company would send items, networks, sourcing, customer orders, and other data to the optimization system, which would process the information and, within about an hour, return an optimized plan ready for execution. This plan could then be directly imported into the company’s ERP and warehouse management systems, allowing for immediate action. This quick turnaround enabled the distributor to maintain agility and responsiveness in their supply chain operations, critical for meeting tight order deadlines and managing complex inventory needs.
6. Project Duration and Impact: The entire project, from initiation to completion, took 25 weeks. This relatively short timeframe was essential given the project’s complexity and the need for a rapid transformation of the distributor’s replenishment planning capabilities. By the end of the project, the distributor had implemented a more agile and efficient replenishment process, allowing them to respond more effectively to changes in demand and supply conditions.
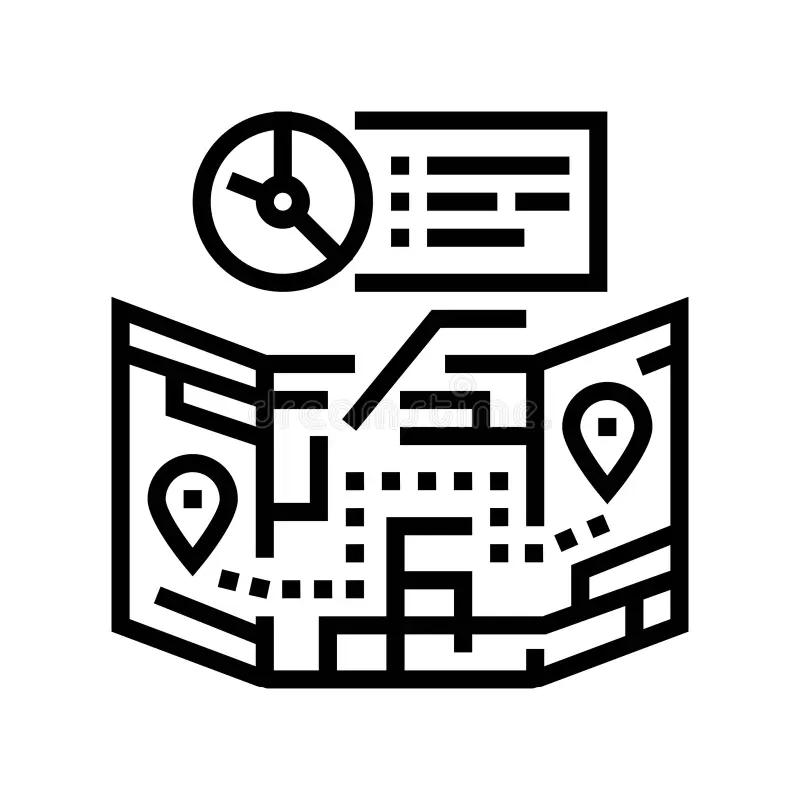
Conclusion
This case study demonstrates the transformative impact of a carefully designed replenishment planning solution tailored to a distributor’s specific needs. By addressing circularity issues, optimizing demand-supply matching, achieving order-level visibility, and implementing real-time optimization, the project enabled the distributor to enhance operational efficiency, reduce costs, and improve service levels across its network. This approach represents a forward-thinking model for other distributors and CPG companies looking to modernize their replenishment planning strategies.
At K3 Group, we specialize in solving complex replenishment optimization challenges. If you’re looking to enhance your supply chain efficiency and streamline your operations, we’re here to help.
About K3 Group
At K3 Group, we specialize in implementing tailored systems that drive efficiency and streamline operations. Our expertise covers a wide range of solutions, including supply chain inventory optimization and inventory planning software to ensure your business is always prepared for demand fluctuations. We support BlueYonder Fulfillment (formerly JDA), Kinaxis RapidResponse, and o9 MEIO systems, integrating them into your overall replenishment planning process to improve accuracy, reduce costs, and enhance service levels across your supply chain. Let us help you optimize your fulfillment and inventory strategies for maximum results.
Discover More on Replenishment Planning Strategies
- Replenishment Planning in a Complex Network – Learn how to manage replenishment across multiple distribution centers and optimize your supply chain network.
- Proactive Replenishment Planning: Stay Ahead of Demand – Discover strategies to anticipate demand changes and maintain optimal inventory levels.
- Case Study: Near Real-Time Replenishment Planning – Explore how near real-time optimization transformed replenishment planning for a leading distributor.
- Scoping a Replenishment Planning Project: Key Considerations – Get a comprehensive checklist of critical topics to address during the scoping phase for a successful project.
- Choosing the Right Replenishment Software – Compare BlueYonder, Kinaxis, and o9 Solutions to find the best software for your replenishment needs.