Scoping a Replenishment Planning Project
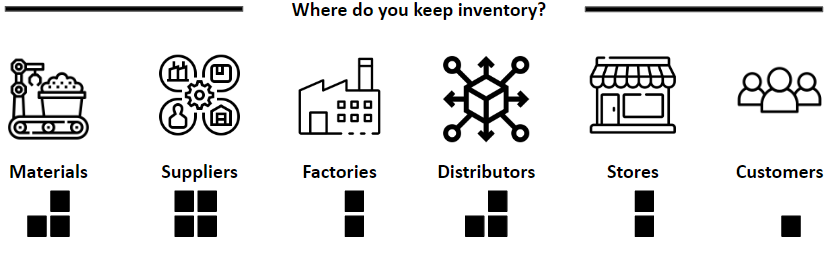
Key Topics Checklist
To ensure a successful replenishment planning project, it’s essential to address several critical topics before starting the implementation during the scoping phase. This is the process we use at K3 to drill into details that will drive an implementation. Each section below provides a brief description and a list of key points to consider.
1. Objectives
Define the project’s overall objectives and set clear expectations for the project timeline and deliverables.
- Identify stakeholders.
- Define project objectives and success criteria.
- Outline project timeline and milestones.
- Identify necessary workshops and planning sessions.
2. Understanding the Supply Chain Network
Gain a comprehensive understanding of the existing supply chain network, its scope, and parameters to identify areas for optimization.
- Review current network design and documentation.
- Define scope of network module (distribution centers, transport modes, lead times).
- Identify sourcing lanes, multiple sourcing factors, and lot-sizing requirements.
- Establish minimum order quantities (MOQ) and other key parameters.
3. Defining the Scope of Supply Chain Planning
Clarify which aspects of the supply chain are within scope, including business units, product types, and master data requirements.
- Determine the business units involved (e.g., domestic, exports).
- Categorize product types and their characteristics.
- Review master data needs for plants, DCs, and distributors.
- Assess current state of master data maintenance.
4. Master Data Requirements
Ensure all master data is complete and accurate to support effective replenishment planning.
- Identify number and types of locations (plants, DCs, suppliers).
- Determine number and classification of items/SKUs.
- Evaluate SKU grouping, prioritization rules, and storable switches.
- Verify data accuracy and completeness.
5. Resource and Capacity Planning
Plan for resource use and capacity constraints to avoid bottlenecks and ensure smooth operations.
- List all resources (production, storage, transportation) and their capacities.
- Identify shared resources and any capacity constraints.
- Define resource capacities at category and SKU levels.
- Establish calendars for production, distribution, shipping, and holidays.
6. Demand and Order Types
Clarify the types of demand and order management rules to ensure proper prioritization and fulfillment.
- Review types of demand (sales orders, forecast orders, backlogs).
- Define sales order rules (lateness, early fulfillment, horizon).
- Establish forecast parameters (levels, allocation, proration, netting).
- Determine planning horizons for different demand types.
7. Demand Prioritization Framework
Develop a framework for prioritizing demand based on various factors to align with business goals.
- Establish prioritization factors (time, product tier, customer tier, demand types).
- Define Linear Programming (LP) layering and demand grouping strategies.
- Set rules for safety stock prioritization.
8. Safety Stock Targets
Define safety stock requirements to maintain inventory reliability and meet customer service levels.
- Set safety stock levels (absolute quantities or days of coverage).
- Align safety stock targets with inventory policies.
9. Supply Data Management
Ensure accurate and comprehensive supply data for effective planning and execution.
- Review inventory data, including locations and sourcing lanes.
- Verify in-transit data management (statuses, delays).
- Confirm fixed supply details (production schedules, outsourcing).
10. Planning Parameters and Granularity
Set planning horizons, granularity, and buckets to align with business needs and industry practices.
- Define planning horizon (e.g., 4-5 months) and granularity (daily, weekly, monthly).
- Establish planning buckets and frozen or firming periods.
11. Planning Objectives and Optimization Goals
Outline the key objectives and goals for the planning process to ensure alignment with business strategy.
- Maximize demand satisfaction and minimize lateness.
- Respect safety stock targets and storage constraints.
- Minimize costs and excess inventory while ensuring just-in-time planning.
12. Outbound Data Interfaces
Define the data needed for outbound processes and ensure smooth integration with existing systems.
- Determine requirements for net production plans, vehicle load plans, and inventory reports.
- Identify exception handling rules and reason codes.
- Plan for seamless integration with ERP and other systems.
13. Scenario Planning
Prepare for potential risks and develop strategies to handle different “What-if” scenarios.
- Plan for various “What-if” scenarios to test strategies.
- Develop contingency plans for unexpected changes in demand or supply.
Conclusion
By thoroughly addressing each of these topics during the scoping phase, you can create a solid foundation for a successful replenishment planning project. At K3 Group, our team is here to help you navigate these complexities and design a solution tailored to your specific needs. Contact us today to learn more.
About K3 Group
At K3 Group, we specialize in implementing tailored systems that drive efficiency and streamline operations. Our expertise covers a wide range of solutions, including supply chain inventory optimization and inventory planning software to ensure your business is always prepared for demand fluctuations. We support BlueYonder Fulfillment (formerly JDA), Kinaxis RapidResponse, and o9 MEIO systems, integrating them into your overall replenishment planning process to improve accuracy, reduce costs, and enhance service levels across your supply chain. Let us help you optimize your fulfillment and inventory strategies for maximum results.
Discover More on Replenishment Planning Strategies
- Replenishment Planning in a Complex Network – Learn how to manage replenishment across multiple distribution centers and optimize your supply chain network.
- Proactive Replenishment Planning: Stay Ahead of Demand – Discover strategies to anticipate demand changes and maintain optimal inventory levels.
- Case Study: Near Real-Time Replenishment Planning – Explore how near real-time optimization transformed replenishment planning for a leading distributor.
- Scoping a Replenishment Planning Project: Key Considerations – Get a comprehensive checklist of critical topics to address during the scoping phase for a successful project.
- Choosing the Right Replenishment Software – Compare BlueYonder, Kinaxis, and o9 Solutions to find the best software for your replenishment needs.